Plastics
Polythene, in all its forms, is still the most widely-used material in rotomoulding: it covers 80 to 90% of all polymers. For all that, other polymers are incorporated into the rotomoulding process to respond to specific problems. Plastics must meet two conditions to be suitable for rotomoulding: High thermal stability and very low material viscosity when melted.
Polythene (PE)
Polythene is a standard, low-cost plastic. There are several types: HDPE (high-density polythene), LDPE (low-density polythene) and co-polymers like LLDPE. It is one of the materials most used in rotomoulding. This material has many interesting features (lightweight, easy to process, resistant to chemicals), especially for manufacturing a variety of products - containers, storage tanks, street furniture, design furniture, marker buoys, etc.
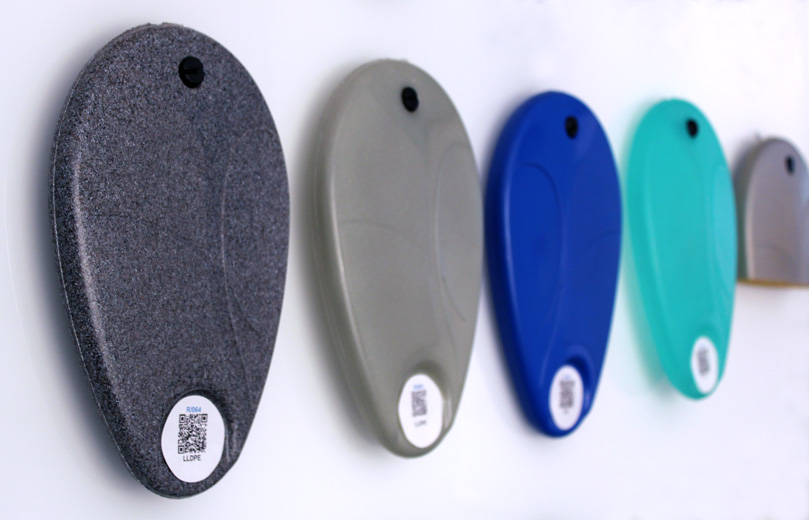
- Shock resistant even when cold
- Abrasion resistant
- Low friction coefficient
- Flexible to rigid grade
- Chemical inertia
- Food contact grade
- Electrical insulation
- Difficult to glue
- Max. use temperatures 50 to 80°C depending on the grade
- Significant shrinkage
Polypropylene (PP)
Polypropylene is a standard, low-cost plastic which delivers mechanical and thermal performances that are superior to polythene. In rotomoulding, it can be found in transport or for infrastructure applications where greater rigidity than PE is required.
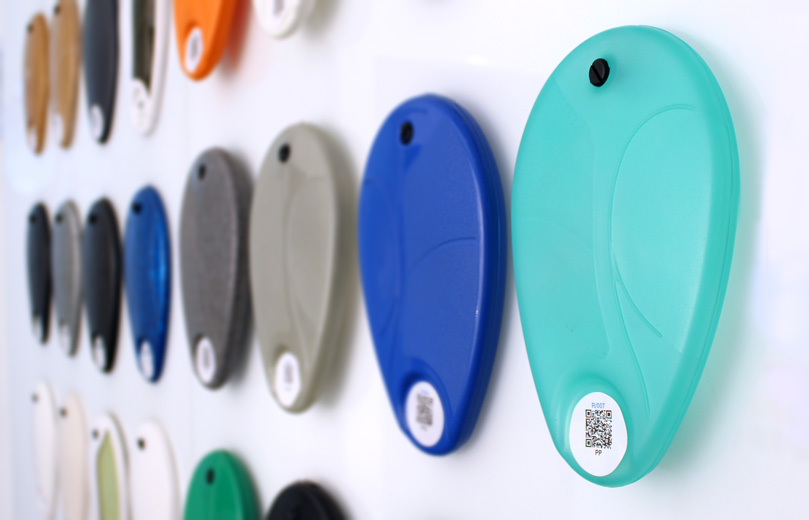
- Properties similar to PE but more rigid
- Very impact resistant
- Temperature resistant (100°C) up to a peak of 140°C
- Good resistance to chemicals
- Very fatigue resistant
- Breaks at low temperature
- Gas permeable (CO2)
- Little resistance to UV
- Little resistance to petrol and strong oxidising agents
- Little resistance to creep
- Substantial shrinkage
Polyamide (PA)
Polyamide is the engineering plastic in vogue. It offers many properties depending on its chemical make-up (rigidity, lightening, chemical resistance, replacement for metal, etc.). In rotomoulding, it is found as PA6 or PA12 and can be used to manufacture oil and fuel tanks for small series vehicles (lorries, tractors, construction machinery, etc.).
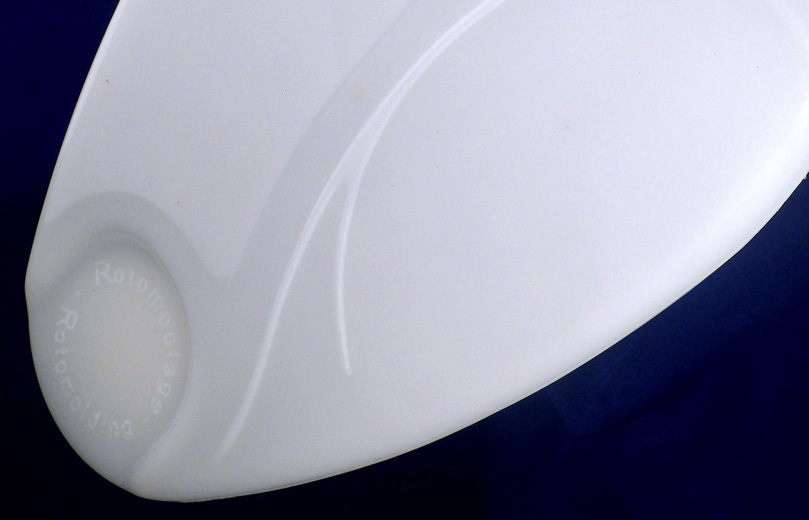
- Low friction coefficient
- Very abrasion resistant
- Good chemical resistance to solvents, oils, hydrocarbons, etc.
- Very fatigue resistant
- Water absorption causing dimensional instability and change in properties
Polycarbonate (PC)
Polycarbonate is the second engineering plastic most produced after polyamide. In rotomoulding, it is used to create transparent parts that are very shock-resistant.
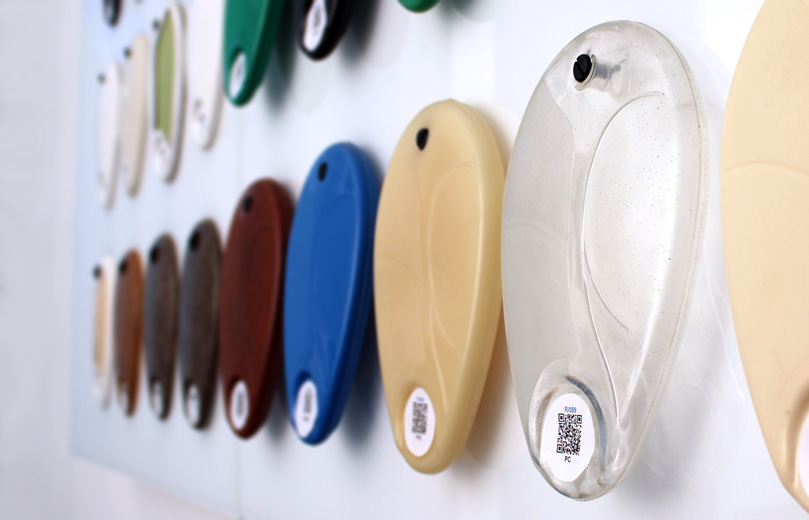
- Excellent transparency
- Glossy surface
- Excellent mechanical properties (rigidity, resistance to impacts, etc.) in a wide temperature range (-150 to 135°C)
- Self-extinguishing
- Limited resistance to hot water
- Limited resistance to UV without additives (yellowing)
- Limited chemical resistance (stress cracking phenomenon)
Polyvinyl chloride (PVC)
PVC is a very low-cost plastic and one of the materials most used in rotomoulding as it can be flexible or rigid. In rotomoulding, it can be used to produce flexible bags or sports items (ball, etc.)
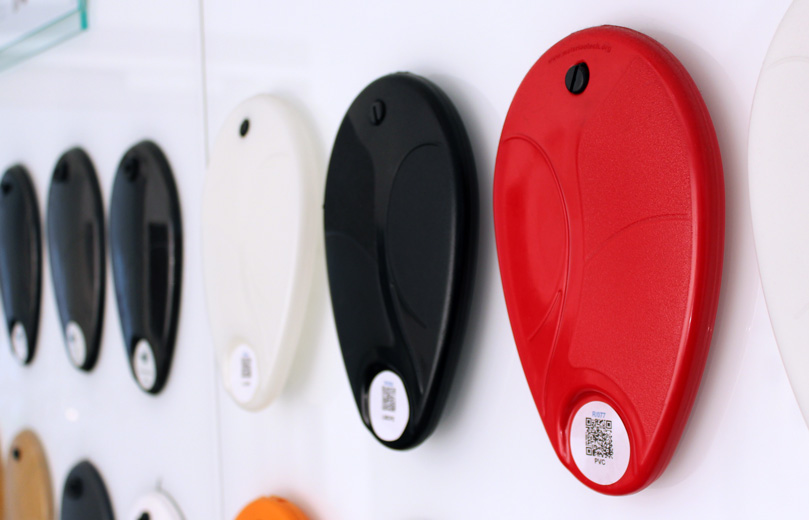
- Very cost-saving
- Good resistance to chemicals
- Intrinsically fireproofed
- Rigid PVC: good mechanical resistance, transparency, relatively good resistance to UV
- Flexible PVC: flexible, transparent
- Tricky to process and can cause the material to deteriorate quickly
- Limited chemical resistance to solvents
- Discolours when exposed to UV for long periods
- Limited temperature resistance
Polyurethane (PU)
Polyurethane is an elastomer material with excellent abrasion resistance. In rotomoulding, it is mainly found in the manufacture of engineering parts that need to be wear-resistant.

- Excellent abrasion resistance
- Resistant to tearing
- Can be transparent
- Resistant to oils
- Fatigue resistant
- Limited resistance to UV
- Limited resistance to chemicals
- Limited temperature resistance
Polyoxymethylene (POM)
Polyoxymethylene is an engineering plastic with excellent chemical and abrasion resistance. It can be used to manufacture reservoirs.
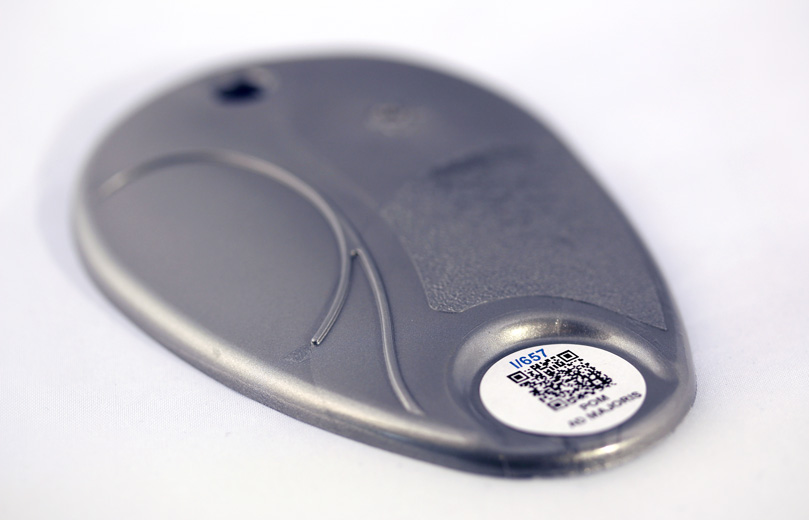
- Highly crystalline
- Excellent abrasion resistance
- Low friction coefficient
- Good resistance to creep
- Good resistance to solvents
- Limited chemical resistance to acids
- Little resistance to UV
- Significant shrinkage
Polyvinylidene fluoride (PVDF)
Polyvinylidene fluoride is a thermoplastic fluoropolymer with excellent resistance to corrosive chemicals. It is basically used to manufacture tanks for the chemical industry.
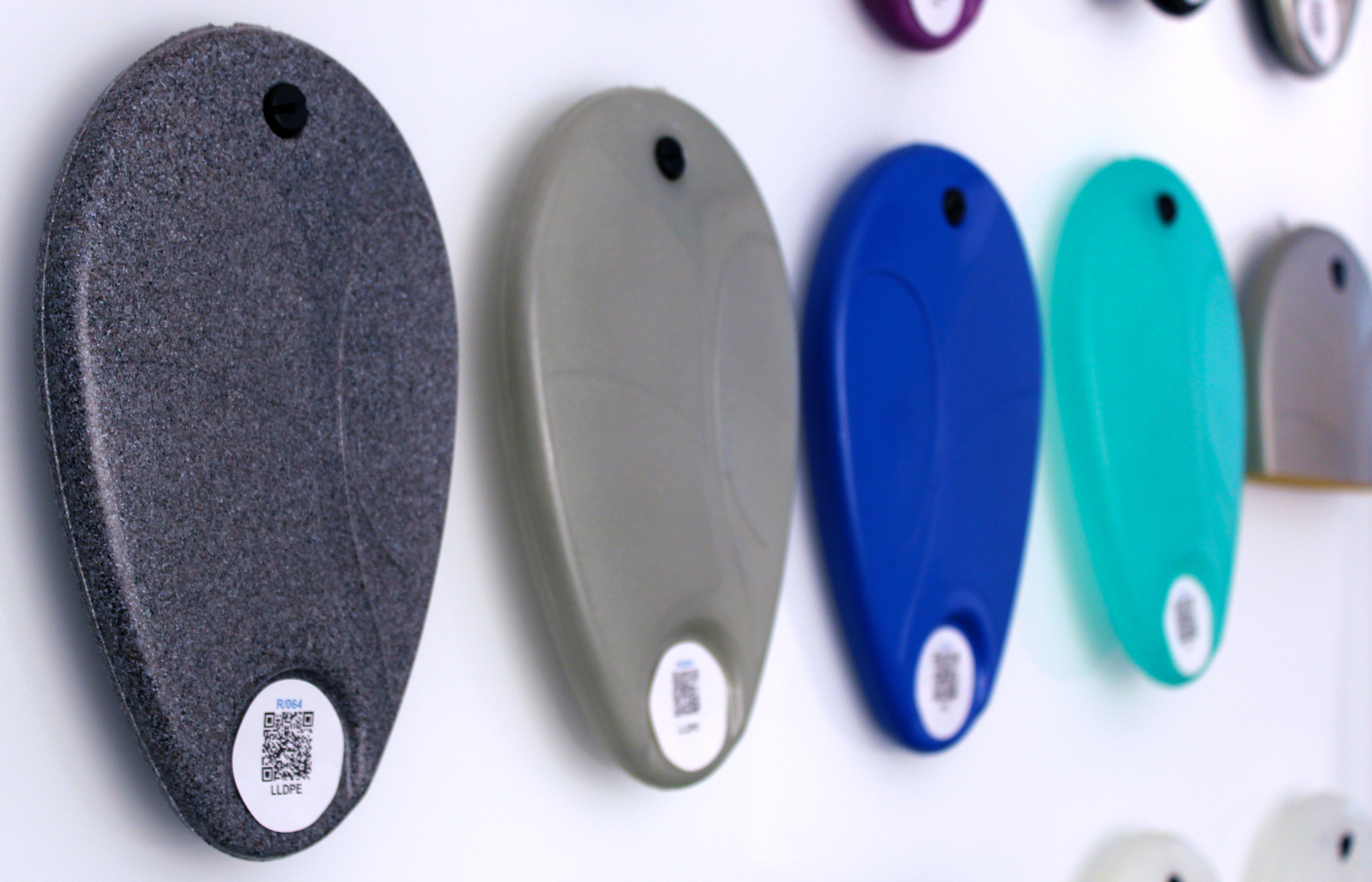
- Good mechanical properties compared with other fluoropolymers
- Good resistance to chemicals
- High dielectric constant
- High piezoelectric and pyroelectric properties
- Fire resistant
- Tends to dissolve under certain polar solvents and basic amines
- Dielectric properties depend on the frequency, limited use as electrical insulation
Thermoplastic polyester elastomer (TPEE)
Thermoplastic polyester elastomer is an engineering plastic between the elastomers and the engineering thermoplastics and provides a good combination of strength and flexibility. It is an alternative to the rigid materials when good shock absorbency is required.
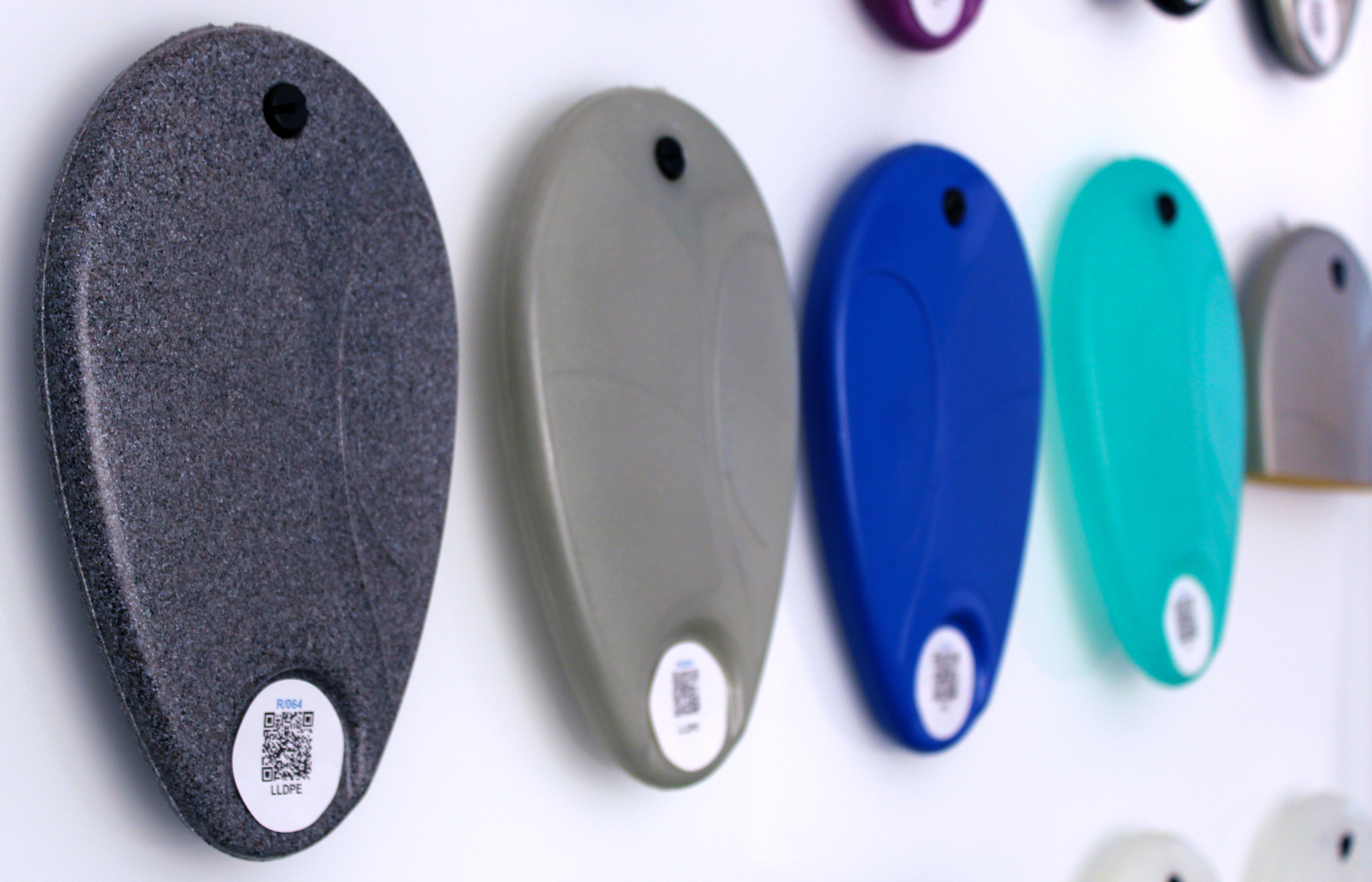
- Very abrasion resistant
- Wide range of temperature use
- Very fatigue resistant
- Highly flexible
- Sensitive to hydrolysis at high temperatures
- Limited resistance to UV
Polystyrene (PS)
Polystyrene is a standard plastic used in many applications. It can produce distinctive-looking parts that are very rigid.
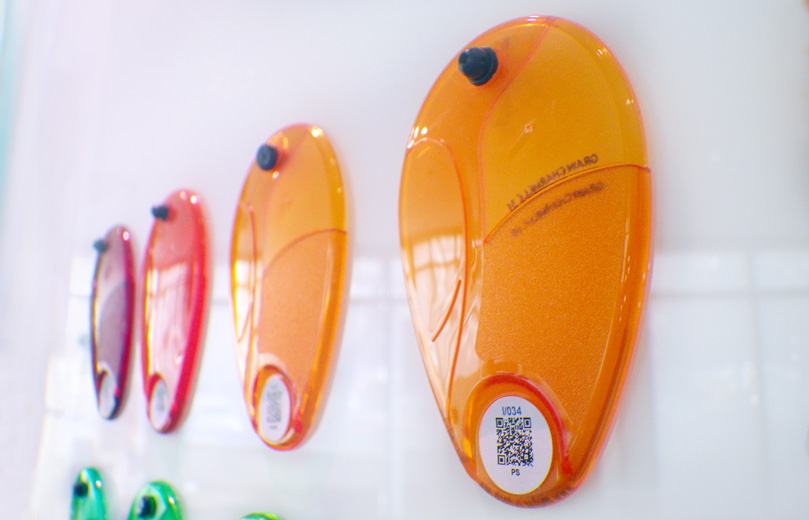
- Cost-saving
- Low shrinkage
- Transparent and glossy
- Extremely rigid
- Good insulation
- Breakable
- Not very abrasion resistant
- Limited resistance to temperature (80°C)
- Limited chemical resistance and sensitive to stress cracking
- Resistance to UV
Polylactic acid (PLA)
Polylactic acid is a biosourced plastic derived from renewable resources (corn, wheat)
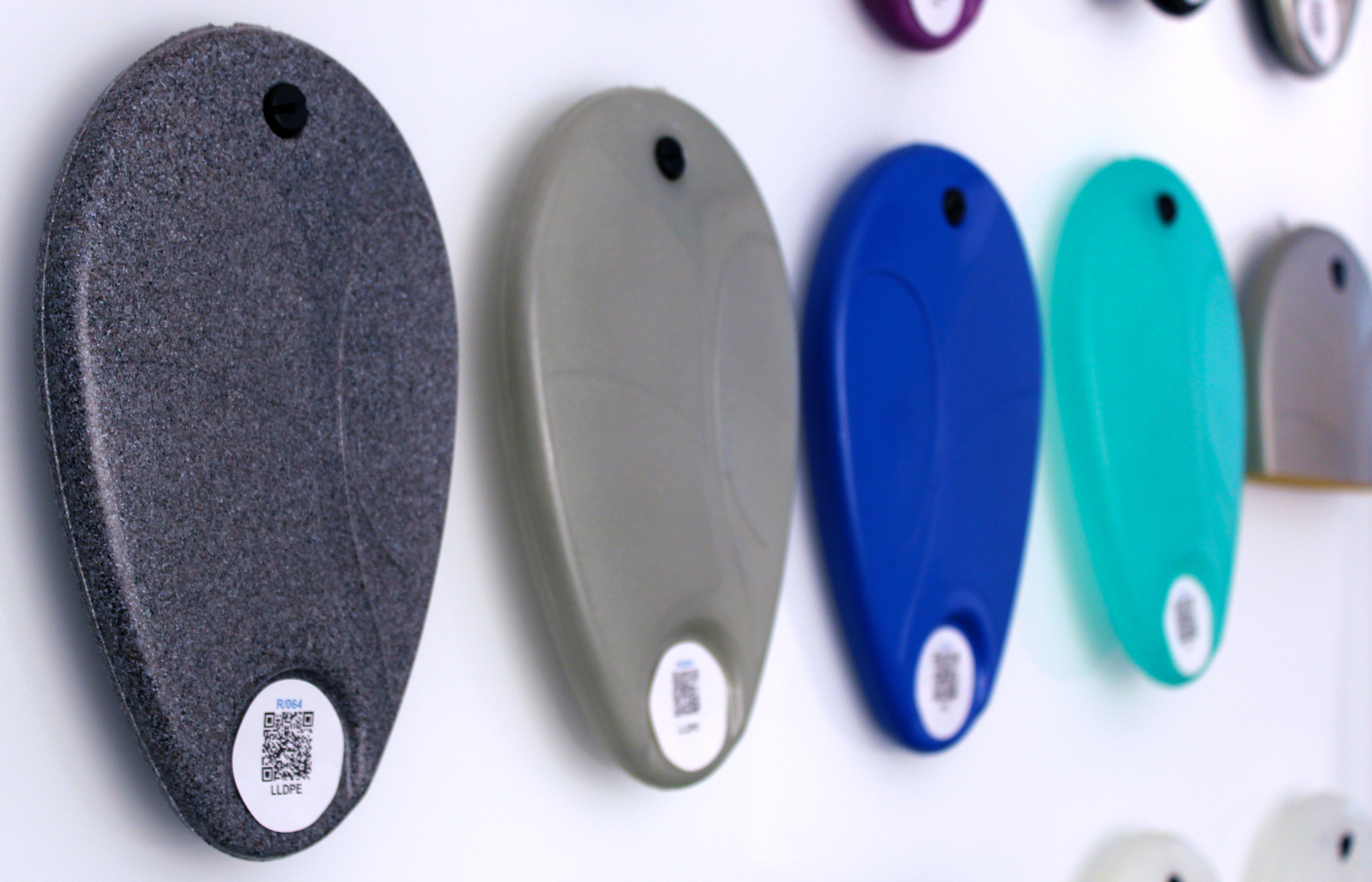
- Transparent
- Rigid
- Good barrier properties against odours
- Reduced environmental impact
- Little resistance to impacts
- Water permeable
- Little resistance to temperature
- More expensive than commodity resins
Ethylene-vinyl acetate (EVA)
Ethylene-vinyl acetate is a flexible plastic based on LDPE with a vinyl acetate monomer. It can be a substitute for flexible LDPE or PVC.

- More flexible, transparent and glossier than LDPE
- Resists perforation better
- Food contact
- Limited mechanical and chemical resistance compared with LDPE
- More flammable than PVC
Composites
Composite materials are a mix of two or more different materials, normally a polymer resin (thermosetting or thermoplastic) and fibres, fillers, cores and/or additives. These materials are being increasingly substituted for metals - they are lightweight, enjoy design flexibility, are mechanically strong and corrosion-resistant. Thermoplastic composites can also be recycled and are easy to assembly, especially by overmoulding, which is difficult with thermosetting composites. These materials are finding an increasing number of applications in the aeronautical, boating and car industries.